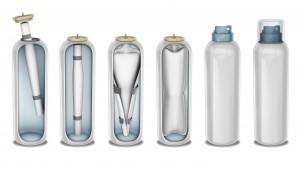
As more companies begin to recognize the benefits of bag-on-valve aerosol technology, we are often asked if bag-on-valve is suitable for their product, and if so, how does the manufacturing process work?
I sat down with Daniel Lagerkvist, Aurena Laboratories’ production manager, to talk about the manufacturing process and how various wound care, skin care, nasal spray, cosmetic and even some food products can be evolved into the modern spray dispensing technology of bag-on-valve (BOV). Below are highlights from our discussion:
Magnus Hedman (MH): As production manager, you’ve been involved in many variations of manufacturing for BOV. Can you start off by telling me what types of products are suitable for this type of aerosol?
Daniel Lagerkvist (DL): Bag-on-valve is incredibly versatile with few limitations. Almost all fluids, including liquids, creams and gels, can be filled into a BOV system. The only requirement is that the product’s viscosity is low enough to get it through the valve stem. Also, BOV does not work well with products that need to be shaken before use.
MH: How does the product get into the can?
DL: The secret is inside the can! There is a rolled-up multi-layered flexible pouch attached to an aerosol valve. During production, compressed air or nitrogen is charged into the can, and an aerosol valve with the bag attached is crimped onto the container. The formulation is forced through the aerosol valve stem to fill the bag. Finally, the actuator and cap are put in place.
MH: What about the packaging? Are different sizes available?
DL: Standard BOV packaging covers a broad range of sizes, from 30mL to 500ml containers. Typically, the cans are standard aerosol aluminium cans with 1 inch openings, with an interior foil-based packaging bag. It’s the bag inside the can that makes it superior to other standard aerosol.
MH: How do you maintain product integrity during the production process?
DL: One of the benefits of BOV is the ability to keep the product separate from the propellant. The product in the bag encompasses 60 per cent of the can’s brim capacity, while the remaining 40 per cent is occupied by the propellant. However, the propellant never comes in contact with the product. This ensures the product formulation stays true to its ingredients, without interference from propellants, flammability or too many preservatives.
MH: You’ve done a great job of explaining the manufacturing and filling process of BOV. Once the product is filled, how is it used?
DL: The end-user simply needs to press on the actuator (the spray button). The product is then squeezed out of the bag by the compressed air or nitrogen, and then out comes the spray, cream or gel. No shaking and no fussing with angles.
MH: Thanks for your time and for helping many of our partners put their products into BOV technology.
DL: We are always up for new challenges and continue to be amazed by the endless possibilities with BOV. I look forward to working with many partners in the future.
Interested in finding out how your product could evolve into bag-on-valve spray technology? Contact the Bag on Valve experts for more information.